In mechanical transmission systems, self-lubricating bearings serve as "silent guardians," enduring dynamic loads while maintaining low friction and wear resistance over the long term without external lubrication. However, engineers often face a dilemma when balancing "performance, cost, and application suitability" among the three mainstream matrix materials: high-strength brass, tin bronze, and aluminum bronze. For example, high-strength brass (such as ZCuZn25Al6Fe3Mn3) is known for its high strength, tin bronze (such as ZCuSn10P1) is low in cost, and aluminum bronze (such as ZCuAl10Fe3) excels in high-temperature resistance. However, improper selection can lead to premature bearing failure or resource wastage.
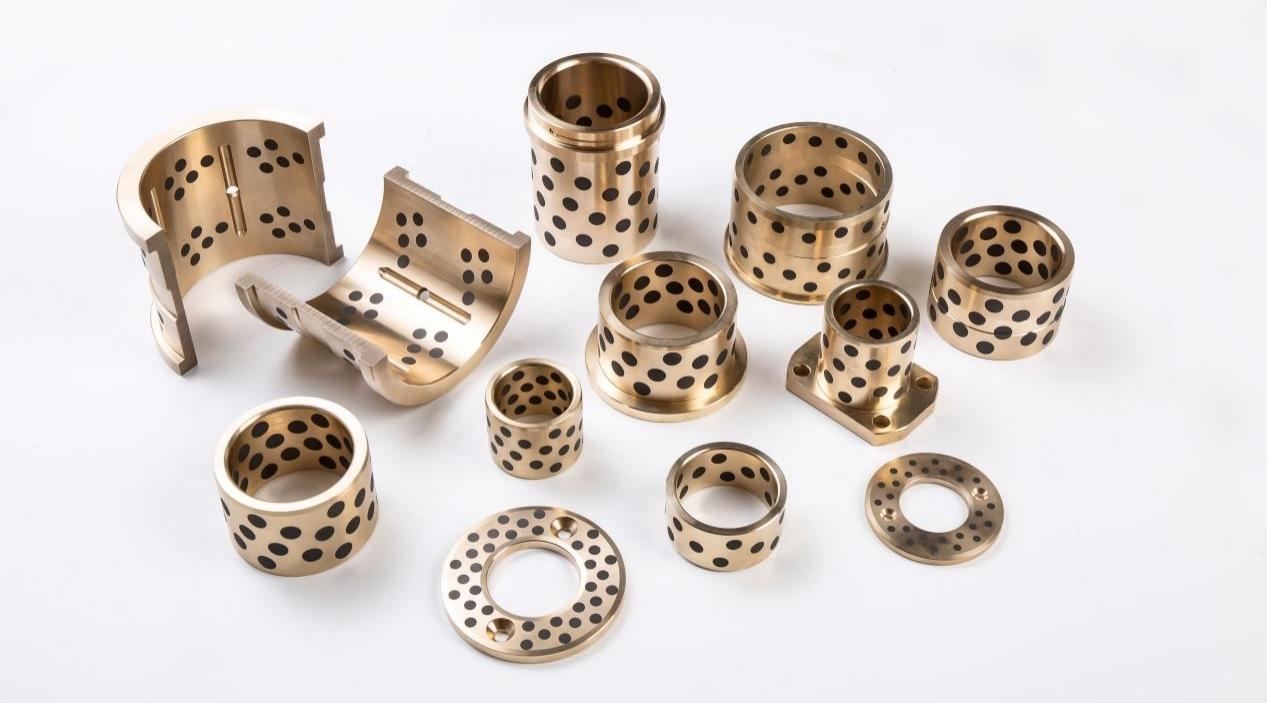
1. Core Performance Comparison and Selection Logic
Mechanical Properties: Strength, Hardness, and Load-bearing Capacity
Indicator
|
High-Strength Brass
|
Tin Bronze
|
Aluminum Bronze
|
Tensile Strength (MPa)
|
650-750
|
200-300
|
500-600
|
Hardness (HB)
|
180-220
|
80-100
|
150-180
|
Ultimate Pressure (MPa)
|
30-50
|
10-20
|
25-35
|
Fatigue Strength (MPa)
|
≥200
|
≥80
|
≥150
|
Selection Suggestions:
• Heavy/shock loads (such as mining machinery, shield machines): Prefer high-strength brass, which has a tensile strength three times that of tin bronze and an ultimate pressure 43% higher than aluminum bronze.
• Low-to-medium speed and light loads (such as textile machinery, conveyor belts): Tin bronze is lower in cost (about 30% less) but requires regular maintenance.
• High-temperature and medium loads (≤400℃): Aluminum bronze, due to its aluminum content, retains 80% of its strength at high temperatures (compared to 65% for high-strength brass).
Tribological Properties: Wear Rate and Lubrication Efficiency
Indicator
|
High-Strength Brass
|
Tin Bronze
|
Aluminum Bronze
|
Dry Friction Coefficient
|
0.08-0.12
|
0.15-0.25
|
0.10-0.18
|
Wear Rate (×10⁻⁴ mm³/(N·m))
|
0.5
|
1.8
|
1.2
|
Lubricant Embedding Volume (%)
|
15-25%
|
10-15%
|
12-20%
|
Selection Suggestions:
• Long-term maintenance-free requirements: High-strength brass has the lowest wear rate (only 28% of tin bronze) and high lubricant embedding capacity, making it suitable for unmanned scenarios like wind turbine pitch bearings.
• Short-term low-cost solutions: Tin bronze has lower initial investment but a higher wear rate, requiring inspection of lubricant release status every 500 hours.
• High-temperature lubrication stability: Aluminum bronze forms a lubrication film 20% faster than high-strength brass at temperatures above 200℃, making it suitable for steel mill roller bearings.
Environmental Adaptability: Temperature and Corrosion Resistance
Indicator
|
High-Strength Brass
|
Tin Bronze
|
Aluminum Bronze
|
Operating Temperature Range (℃)
|
-50~300
|
-50~200
|
-50~400
|
Salt Spray Corrosion Resistance (hours)*
|
≥720
|
≥240
|
≥1000
|
Acid and Alkali Resistance (pH 2-12)
|
Excellent
|
Moderate
|
Excellent
|
*Note: Salt spray test standard ASTM B117, 5% NaCl solution.
Selection Suggestions:
• Marine/chemical environments: Aluminum bronze has the best salt spray resistance (no pitting after 1000 hours), followed by high-strength brass; tin bronze is prone to dezincification corrosion and requires surface coating.
• Wide temperature fluctuations: Aluminum bronze maintains the best strength stability within the range of -50~400℃, followed by high-strength brass (hardness decreases by 15% after 300℃).
2. Economic Analysis and Life Cycle Cost
Initial Cost and Maintenance Expenses
• Material price per ton (2023 average): Tin bronze (68,000 yuan) < High-strength brass (72,000 yuan) < Aluminum bronze (85,000 yuan).
• Maintenance interval: High-strength brass (1200 hours) > Aluminum bronze (800 hours) > Tin bronze (500 hours).
• Comprehensive cost case: A cement plant switched to high-strength brass for its vertical mill bearings, reducing total costs (including replacements and downtime losses) by 41% over three years, while the aluminum bronze option reduced costs by 28%.
Failure Risk and Hidden Costs
• Tin bronze: Cost-effective under light loads, but wear rate increases dramatically under heavy loads, with a sudden failure risk three times higher than that of high-strength brass (source: "Heavy Machinery," 2023, Issue 4).
• Aluminum bronze: Excellent high-temperature performance but difficult to cold work, with processing costs 25% higher than those of high-strength brass.
3. Decision-Making Flowchart and Quick Selection Guide
Determine Application Priority:
Heavy/shock loads? → High-strength brass
High temperatures (>300℃)? → Aluminum bronze
Severe corrosion environment? → Aluminum bronze or high-strength brass
Low cost/light loads? → Tin bronze
Verify Lubrication Requirements:
High maintenance-free requirements? → High-strength brass (high lubricant embedding capacity)
Regular maintenance possible? → Tin bronze or aluminum bronze
Life Cycle Cost Calculation:
Considering equipment downtime losses and replacement frequency, select the option with the lowest overall cost.
The essence of selection is a "trade-off between performance requirements and economics":
• High-strength brass is a "versatile player" for heavy loads, corrosion resistance, and maintenance-free scenarios, suitable for high-end equipment pursuing long-term reliability.
• Tin bronze, with its low cost, remains competitive in light-load, low-speed, and short-term projects.
• Aluminum bronze locks in special application demands with its "single advantages" in high-temperature resistance and corrosion resistance.
In future trends, high-strength brass, further enhanced through nanomodification (such as adding silicon carbide particles), may become a more universally applicable solution.
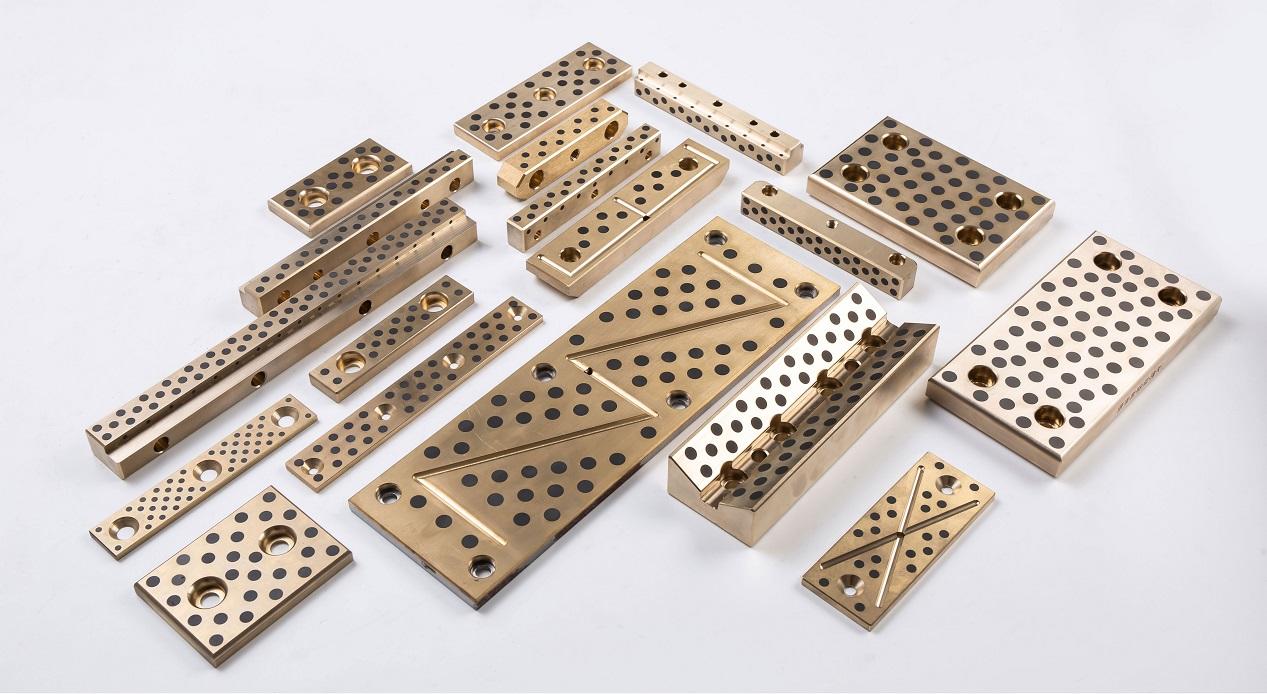
Please feel free to contact Zhejiang Mingxu Machinery Manufacturing Co., Ltd.: [email protected] for more advice on material selection for self-lubricating bearings.
Contattaci